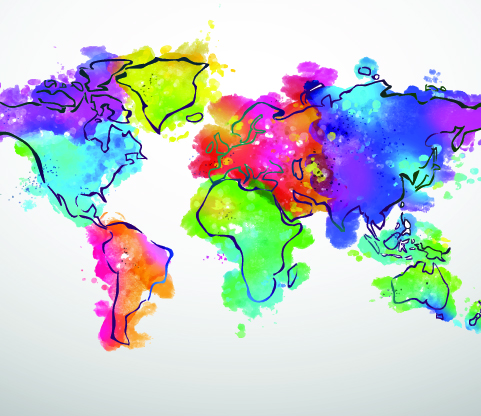
-
Avient Specialty Inks
Looking for a Distributor?
-
Services
Looking for Ink Resources?
- Resources
- Distributors
Rutland™ makes the screenprinting process easier, more attractive and more profitable.
Rutland is a leading brand of specialty inks for the textile industry. It is well known in the global screen printing industry for a continuous focus on innovative and quality inks that our customers continue to value and trust. Our global footprint ensures that the right product and support is available whenever and wherever needed – around the world and around the clock.
Since 1962, Rutland has developed products to make the screen printing process easier, more attractive and more profitable. Rutland developed the industry’s first printer-friendly mixing system using finished inks and high-performance specialty inks accessible through a global network of qualified Rutland distributors.
Rutland’s cutting-edge chemistries are why internationally recognized brands of athletic and fashion apparel choose us to manufacture and supply high-quality inks for their products. Rutland produces hundreds of standard inks, offering exceptional performance and value for screen printers.
Rutland inks are ready to tackle everything from the challenging printing jobs to the day-to-day work
Comprehensive system of white inks, ready-for-use and mixing system colors, special effects and additives
Integrates with our IMS 3.0 ink management cloud-based solution for managing color and inventory in the textile screen printing market
Printers expect repeatable results and Rutland inks have proven to answer the call
From white inks to ready-for-use colors, Rutland has innovative and simple solutions
Streamline Pantone® color matching using our finished ink mixing system M3 or our C3 color booster system
Rutland™ ink bases offer printers more freedom of choice to modify performance and help to minimize inventory
Rutland™ Chill chemistry provides printers a flexible cure range from 250°F/121°C to the standard plastisol curing temperature of 320°F/160°C